Share
Pin
Tweet
Send
Share
Send
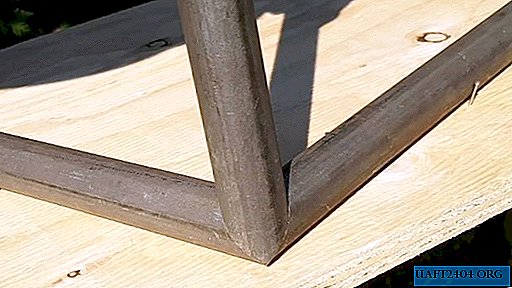
Will need
Consider this method of connection on the example of round pipes. For successful work, we need to stock up on the following tools and materials in advance:
- a piece of pipe with a diameter of 75 mm and a length of at least 1000 mm;
- pendulum saw with rotary table;
- removable clamp;
- tape measure with a measuring tape;
- marker and metal plate;
- electric or gas welding apparatus;
- flat horizontal surface.
The procedure for performing double corner joints
For this work, some special skills are not required, but all operations, and, first of all, marking and measuring, must be performed accurately and accurately.
1. We lay the pipe on the table of the pendulum saw, measure out the necessary length with a tape measure, put a marker on the marker, clamp the workpiece with a clamp and saw off the first pipe section. Repeat this operation twice more and get three tube blanks with a diameter of 75 mm and a length of 300 mm. In other cases, the dimensions may be arbitrary.


2. We rotate the table of the pendulum saw by 45 degrees and fix it in this position.
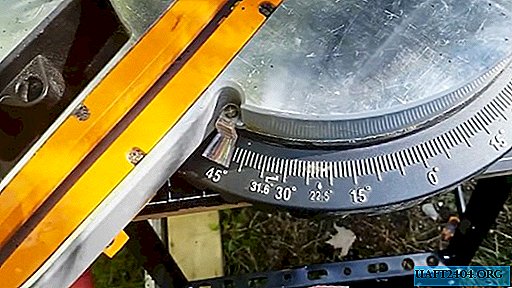
3. We fix each of the three pipe segments on the table of the pendulum saw with a fixed rotation and make a cut from one end that will be exactly 45 degrees.


4. Without changing the position of the pipe blanks after the first cut, at the ends we mentally draw the vertical and horizontal diameters, noting their intersection with the pipe body by strokes by means of a marker.
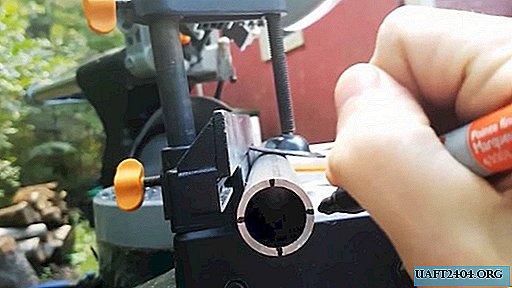
5. Weaken the fastening of the pipe on the table of the pendulum saw and, without changing the longitudinal position, turn it 1/4 circle or 90 degrees clockwise and re-fix the workpiece by checking the absence of longitudinal displacement using a flat metal plate.

6. We make one more cut of the end with a cut already completed. The result is an intricate configuration - the result of the interaction of the flat disk of the pendulum saw and the cylindrical surface of the pipe. We subject all three pipe blanks to this operation.

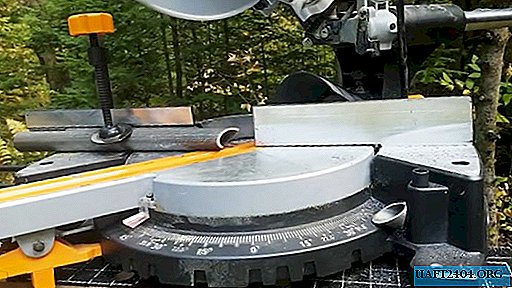

7. We lay two blanks on a horizontal surface with cuts to each other and bring them together until they touch on the desired line. If the marking was correct, and the cuts were made efficiently, then the blanks form a flat angle exactly equal to 90 degrees.
8. Without changing the position of the pipe blanks, we “grab” them from the inside by electric or gas welding, thereby fixing them relative to each other.

9. It remains only, at the junction of two horizontally arranged pipes, to attach a third element vertically from above. If its marking and a segment were made precisely, then the upper workpiece with all its end points will exactly coincide with the place intended for it.
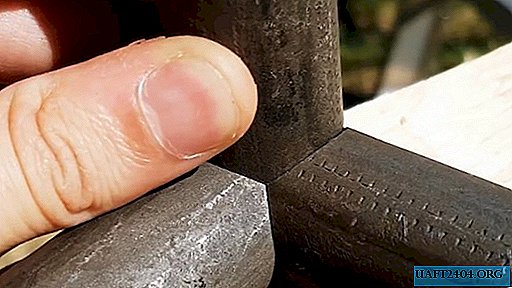
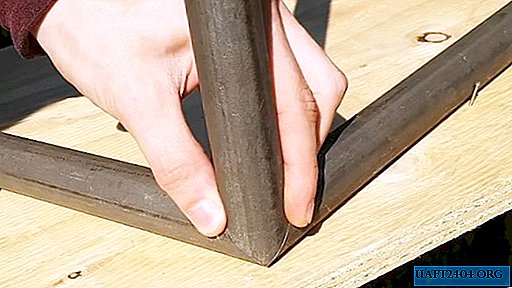
… and in the end
To eliminate injuries and damage, it is necessary to use personal protective equipment: gloves and a welding mask.
Share
Pin
Tweet
Send
Share
Send